Understanding the Role of Injection Molding Manufacturers
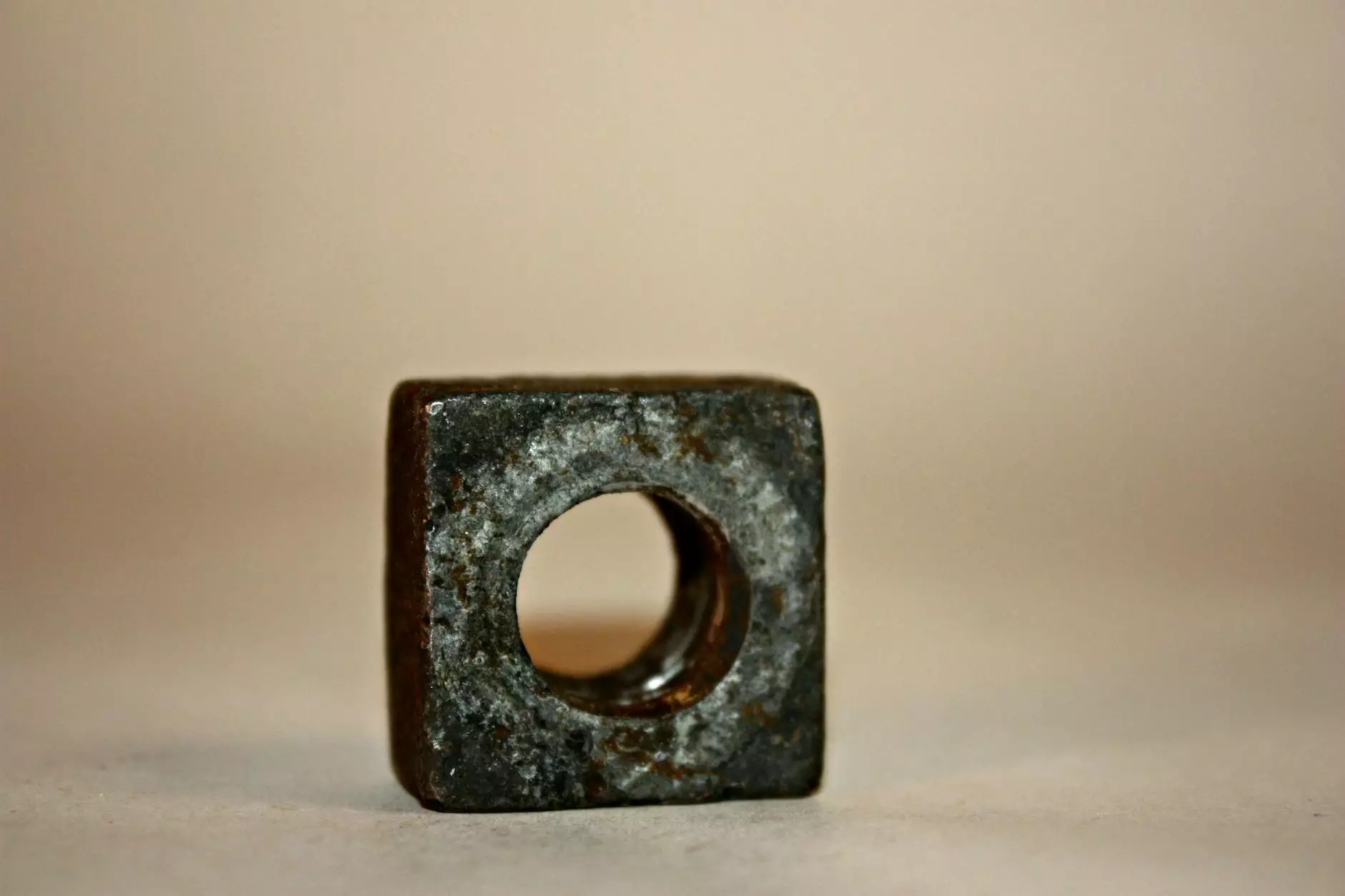
In today's highly competitive manufacturing landscape, injection molding manufacturers play a pivotal role in the production of various plastic components. From automotive parts to consumer goods, the significance of this technology cannot be overstated. This comprehensive article will delve into the intricacies of injection molding, the benefits it offers, and why partnering with the right manufacturer is essential for success in your business.
What is Injection Molding?
Injection molding is a manufacturing process used for producing parts by injecting molten material into a mold. This method is widely used for creating plastic parts and has revolutionized the way businesses produce components efficiently and at scale. The process involves several key steps:
- Material Selection: The first step involves selecting the appropriate thermoplastic resin or thermosetting polymer.
- Heating: The selected material is heated until it reaches a molten state.
- Injection: The molten plastic is injected into a pre-designed mold under high pressure.
- Cooling: Once the mold is filled, the material is allowed to cool and solidify.
- Release: The mold is opened to release the finished part.
The Advantages of Working with Injection Molding Manufacturers
Choosing to work with injection molding manufacturers offers numerous advantages for businesses, particularly in industries where precision, efficiency, and scalability are paramount. Here’s why this process is integral to modern manufacturing:
1. Cost Efficiency
One of the most significant benefits of injection molding is its cost efficiency, especially for high-volume production. Once the initial mold is created, the cost per unit decreases substantially with increased production rates. This makes it an economically viable option for manufacturers looking to scale.
2. Precision and Quality
Injection molding enables manufacturers to produce components with high precision and consistency. The ability to create complex shapes while maintaining tight tolerances is crucial for industries such as automotive and aerospace, where quality is non-negotiable.
3. Material Versatility
Injection molding supports a wide range of materials, including various plastics and elastomers. This versatility allows businesses to choose materials that best fit their product requirements, whether it be strength, flexibility, or heat resistance.
4. Fast Production Speeds
Thanks to the efficiency of the injection process, manufacturers can produce large quantities of parts quickly. This fast turnaround time is essential for companies that need to respond to market demands swiftly.
5. Reduced Waste
Injection molding minimizes waste production. The process uses only the material necessary to fill the mold, making it a more sustainable option compared to other manufacturing methods that may generate excess scrap material.
Choosing the Right Injection Molding Manufacturer
The success of your product development can depend significantly on your choice of a manufacturer. Here are crucial factors to consider when selecting the right injection molding manufacturers:
1. Experience and Expertise
Partnering with manufacturers that have years of experience in the industry ensures you benefit from their knowledge and best practices. Look for companies that specialize in your specific industry or application.
2. Quality Assurance Protocols
Quality is paramount in manufacturing. Ensure that potential manufacturers have stringent quality assurance measures in place, including certifications such as ISO 9001 to guarantee the reliability of their products.
3. Technology and Equipment
Modern techniques and state-of-the-art machinery can significantly enhance production efficiency and part quality. Assess the technology used by manufacturers to ensure they can meet your production standards.
4. Customization Capabilities
Every product is unique, and your manufacturer should be able to offer custom solutions tailored to your specific needs. Discuss their capacity for customization during your selection process.
5. Customer Support
Effective communication and support are vital to a successful partnership. Choose manufacturers that provide excellent customer service and are willing to work collaboratively at every stage of production.
Injection Molding Applications Across Industries
The applications of injection molding are virtually limitless. Here are some significant industries that rely heavily on injection molding manufacturers:
1. Automotive Industry
Injection molding is extensively used in the automotive sector for producing components such as dashboards, interior trims, and engine parts. The precision of injection molding helps in meeting the strict regulatory and safety standards required in this industry.
2. Consumer Electronics
From smartphone casings to intricate components in gadgets, injection molding is instrumental in the consumer electronics industry. The ability to produce lightweight, complex parts is essential for modern electronic devices.
3. Medical Devices
The medical industry demands high-quality and sterile components, which is where injection molding excels. Manufacturers create parts for syringes, surgical instruments, and various medical devices, adhering to stringent industry regulations.
4. Packaging
Injection molding is a common method for producing packaging components such as containers and closures. The efficiency and precision of the method ensure that packaging is both functional and aesthetically pleasing.
5. Household Products
Many everyday household items are produced using injection molding, including kitchen utensils, furniture components, and toys. The versatility of materials used allows for a wide variety of products.
The Future of Injection Molding
As technology advances, the injection molding industry is evolving. Here are some trends shaping the future of injection molding manufacturers:
1. Sustainable Practices
There is a growing demand for sustainable production methods. Many manufacturers are adopting greener practices, such as using recycled materials and optimizing processes to minimize waste and energy consumption.
2. Automation and Smart Manufacturing
Automation is revolutionizing injection molding, making production faster and more consistent. Smart manufacturing techniques, including the Internet of Things (IoT) and Industry 4.0 technologies, are enhancing operational efficiency.
3. 3D Printing Integration
Some manufacturers are integrating 3D printing technologies with injection molding processes. This combination allows for rapid prototyping and custom components that can streamline product development cycles.
4. Advanced Materials
Innovations in materials science are leading to the development of advanced polymers that offer improved properties, such as resistance to heat and chemicals. These materials will expand the applications of injection molding even further.
Conclusion
In summary, injection molding manufacturers are an essential component of the modern manufacturing ecosystem, providing efficient, precise, and cost-effective solutions across various industries. By understanding the advantages of this process and the critical factors involved in choosing a manufacturer, businesses can ensure their success and remain competitive in a rapidly evolving market. As technology continues to advance, the future of injection molding looks promising, filled with opportunities for innovation and efficiency.
For businesses looking to partner with reliable injection molding manufacturers, it’s vital to consider quality, experience, and the ability to cater to your specific needs. By investing in a quality partnership, you're not just choosing a manufacturer; you're contributing to the growth and development of your business.